Navigating the Terrain of Heavy Equipment Maintenance
Maintaining heavy equipment is like being a superhero for big machines used in heavy-duty operations like construction sites and mines. Picture it as taking care of giants that do the heavy lifting – literally! The term we use for this work is “heavy equipment maintenance.” Now, why is it such a big deal?
Think of these enormous machines as the basis of heavy-duty operations. They are the muscle that moves mountains, construct skyscrapers, and extract valuable resources from the earth. With them, these tasks are possible. Now, here’s where the superhero part comes in – heavy equipment maintenance is like giving these giants a spa day.
Imagine if your toys started getting rusty, loose screws, or worn-out parts. They wouldn’t work as well. Well, the same goes for these giants. They experience a lot of stress when working heavy jobs all day. If we don’t take care of the wear and tear that results from this stress, issues will eventually arise.
All of this can lead to parts getting worn down, which is where heavy equipment maintenance steps in. Adhering to a regimen that tightens all fasteners, swaps out worn-out gears, and ensures everything is in top condition is essential.
Let’s break it down. Heavy-duty operations put intense pressure on these machines. They face extreme weather, rough terrain, and challenging tasks.
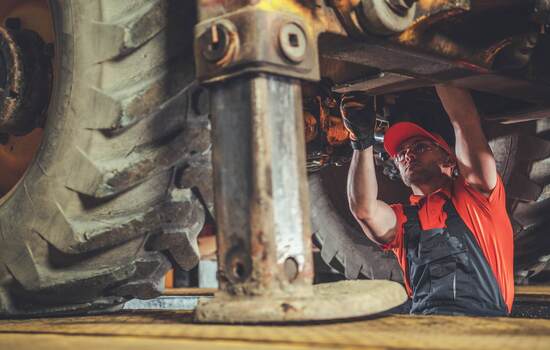
Heavy Equipment Maintenance Recommendations
Inspection Routines
For heavy-duty equipment to operate smoothly and last a long time, routine inspection procedures are essential. These represent an organized and routine inspection of different parts and systems, including brakes, safety features, hydraulic systems, engines, and hydraulic systems.
When discussing heavy equipment maintenance it is impossible to minimize the importance of pre-operation inspections. This procedure is the first line of defense against possible problems. Operators perform visual inspections, functional tests, and timely correction of any anomalies. They can spot new problems early on and stop them from becoming bigger. Problems that could cause expensive downtime by following routine inspection protocols. Operators follow detailed checklists made specifically for each kind of equipment.
Additionally, by keeping equipment in good working order, accidents and malfunctions are reduced. This proactive approach helps to improve safety on building sites and in industrial environments. The foundation of efficient preventive heavy equipment maintenance is ultimately routine inspection procedures.
Downtime Reduction Strategies
To minimize downtime and avoid expensive repairs, businesses should establish regular maintenance schedules and inspections.
First, one key strategy is implementing a proactive maintenance approach. Instead of waiting for components to fail, scheduled inspections and preventive measures are employed to identify potential issues before they escalate. Additionally, predictive maintenance, based on data analytics, helps anticipate when components are likely to fail, allowing for timely replacements and reducing unexpected breakdowns.
Second, to guarantee correct handling and early warning sign identification. For this, regular training programs for maintenance personnel and equipment operators are essential. Educated personnel can address minor issues quickly, preventing them from becoming major issues. It also encourages a group responsibility for equipment care when an organization adopts a preventive heavy equipment maintenance culture.
Third, strategic spare part management is another vital aspect. Having a well-organized inventory of critical components reduces the time needed for repairs. Establishing partnerships with reliable suppliers ensures quick access to genuine parts, minimizing downtime during maintenance activities.
Environmental Considerations in Maintenance
Environmental consciousness is becoming more important in the field of heavy equipment maintenance. As industries recognize their ecological impact, adopting environmentally friendly maintenance practices has become imperative. The appropriate disposal of waste produced during maintenance operations is one important factor. Ensuring the responsible handling and disposal of lubricants, fluids, and worn-out parts prevents environmental contamination.
Using eco-friendly substitutes in maintenance procedures is also becoming more and more important. This includes the adoption of biodegradable lubricants and environmentally safe cleaning agents. Selecting equipment with energy-efficient features also contributes to reducing the overall environmental footprint.
Again, implementing preventive measures is important to avoid leaks and spills. Hazardous contaminants can be kept out of the soil and water sources by routine leak detection checks and prompt repairs. When possible, recycling and reusing materials align with sustainable maintenance practices.
Consequences of Neglecting Heavy Equipment Maintenance Procedures
Failure to follow proper maintenance procedures and inspections in heavy equipment. This can have serious consequences, affecting both operational efficiency and safety. One immediate consequence is increased downtime. Without regular maintenance, equipment is prone to breakdowns and malfunctions, resulting in unscheduled and prolonged downtimes. This causes delays in project timelines, lowers productivity, and incurs additional repair costs.
Neglecting heavy equipment maintenance also causes significant safety risks. Heavy equipment operates in hazardous environments, and any malfunction or failure can result in accidents, injuries, or even fatalities. Regular inspections and maintenance protocols are crucial for identifying potential issues before they escalate into hazardous situations. This not only safeguards the well-being of operators and workers but also protects the surrounding environment.
On top of that, the financial implications of neglecting maintenance are substantial. The cost of reactive repairs and replacements is often higher than the expenses associated with preventive maintenance.
Long-term consequences exist in addition to immediate financial and safety concerns. Neglected heavy equipment maintenance accelerates the wear and tear of equipment components, reducing their lifespan.
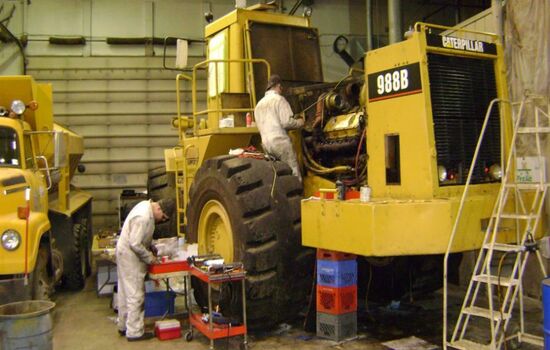
Operational Resilience through Proactive Maintenance
In conclusion, implementing a comprehensive approach that combines proactive maintenance, advanced monitoring technologies, continuous training, and strategic spare parts management is key to reducing downtime in heavy equipment operations.
In addition, incorporating environmental considerations into heavy equipment maintenance necessitates a comprehensive approach. From waste management to the use of eco-friendly products and preventive measures, these practices contribute to a more sustainable and environmentally responsible operation.
And, finally, neglecting appropriate maintenance procedures and inspections in heavy equipment can result in a cascade of negative consequences. From increased downtime and safety risks to financial strain and reputational damage.